Introduction
When it comes to bulk packaging solutions, Ad*Star bags have gained global recognition for their strength, durability, and efficiency. Developed using polypropylene-based woven fabric and specialized heat-sealing technology, these bags are widely used for packaging cement, fertilizers, animal feed, and more. However, as sustainability becomes a defining concern in industrial packaging, it’s essential to look beyond performance and explore the entire life cycle of an Ad*Star bag—from its creation to its end-of-life impact.
This blog delves into the life cycle analysis (LCA) of an Ad*Star bag, evaluating each stage—from raw material sourcing to final disposal—and assessing its environmental footprint along the way.
The Life Cycle Analysis (LCA) of an Ad*Star Bag
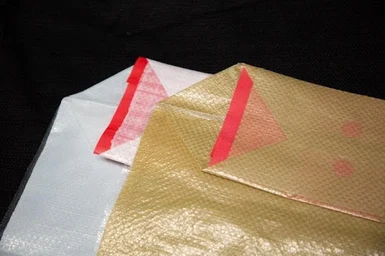
Stage 1: Raw Material Extraction and Production
The journey of an Ad*Star bag begins with polypropylene (PP), a petroleum-based thermoplastic polymer. PP is favored for its strength, flexibility, and resistance to moisture and chemicals, making it ideal for heavy-duty applications.
Environmental Impact:
- High energy input is required to extract crude oil and refine it into polypropylene resin.
- Carbon emissions are significant during this stage due to the fossil fuel-based origin of PP.
- However, PP has a lower density compared to other plastics, which means less material is needed for high-strength applications, partially offsetting its footprint.
Stage 2: Manufacturing and Fabrication
In this stage, polypropylene is extruded into tapes, woven into fabric, and then cut, printed, and assembled into Ad*Star bags using hot air welding or ultrasonic sealing—a process that eliminates the need for glue or stitching.
Key Advantages:
- No adhesives or sewing threads are used, reducing auxiliary material waste.
- High-speed automation makes the process efficient and cost-effective.
- The resulting bag is lightweight yet strong, often outperforming traditional paper sacks in durability tests.
Environmental Considerations:
- Manufacturing consumes electricity and heat energy, contributing to carbon emissions.
- PP off-cuts and trimmings, if not recycled in-house, can lead to production waste.
Stage 3: Transportation and Distribution
Due to their low weight and compact stacking, Ad*Star bags are space-efficient during transport, which reduces fuel consumption per unit.
Environmental Upside:
- Lower transportation emissions compared to heavier alternatives like multi-ply paper or jute bags.
- Minimal packaging needed for shipping—stacked bags can be palletized without excess wrapping.
Stage 4: Usage and Performance
Ad*Star bags are primarily used in construction, agriculture, and industrial sectors, where they hold heavy, dry goods such as cement or fertilizer. Their resistance to moisture and tearing ensures that fewer bags are wasted or damaged during handling.
Benefits During Use:
- Reduces product loss due to bag failure.
- UV-resistant versions extend shelf life in outdoor environments.
- Reusable in some secondary applications (e.g., storage, covering materials).
Stage 5: End-of-Life and Disposal
Here’s where sustainability becomes more complex. After fulfilling their purpose, most Ad*Star bags face two common disposal outcomes: landfilling or incineration. While technically recyclable, polypropylene bags often do not enter proper recycling streams, especially in developing markets.
Challenges:
- Contamination from cement, fertilizers, or food-grade materials can make recycling impractical.
- Lack of segregated collection systems means many bags end up in landfills.
- When incinerated, PP burns cleanly but releases CO₂, contributing to greenhouse gas emissions.
Opportunities:
- In areas with good infrastructure, PP bags can be mechanically recycled into products like buckets, piping, or even new fabric.
- Reuse by local communities for non-packaging applications (e.g., temporary roofing, ground covers) extends their useful life.
Circular Economy Potential: Can Ad*Star Bags Be More Sustainable?
Ad*Star bags have a longer functional lifespan and better protective performance than many alternatives. While they are not biodegradable, they are durable and recyclable—two traits that can contribute positively to a circular packaging model if recovery systems are in place.
Sustainability Enhancements Include:
- Closed-loop recycling programs for industrial users
- Post-consumer collection systems by municipalities
- Encouraging reuse before disposal or recycling
- Improved labeling to educate users on proper disposal methods
Life Cycle Comparison: Ad*Star vs. Paper and Jute Bags
When considering environmental impact across the life cycle, Ad*Star bags often outperform alternatives in transport efficiency, product protection, and longevity.
Bag Type | Water Use | CO₂ Emissions | Recyclability | Durability |
---|---|---|---|---|
Ad*Star (PP) | Low | Moderate | High (if collected) | High |
Paper Sack | High | High (due to energy-intensive paper production) | Biodegradable | Moderate |
Jute Bag | High | Low | Biodegradable | Low to Moderate |
Ad*Star’s durability and lower water usage give it a unique sustainability advantage—especially in high-volume, long-distance applications.
Also Read: Sustainability and Strength: The Environmental Edge of AdStar Bags
Conclusion
The Ad*Star bag is a packaging innovation that performs impressively across its life cycle—particularly in durability, weight efficiency, and transport emissions. However, its end-of-life challenges remain a weak spot, primarily due to gaps in recycling infrastructure and post-consumer collection.
For industries and governments seeking a balance between functionality and sustainability, improving the reuse and recovery stages of Ad*Star bags could be key. By closing the loop on this versatile product, we can reduce its environmental impact and move closer to a circular packaging economy.