Introduction
In today’s environmentally conscious world, packaging is under greater scrutiny than ever before. Businesses and consumers alike are seeking solutions that balance functionality with sustainability. One packaging product that has gained significant traction across industries—especially for cement, fertilizer, and grains—is the Ad*Star bag. But as its usage expands, one important question emerges: Are Ad*Star bags recyclable?
Let’s explore the recyclability of Ad*Star bags, their environmental impact, and how they fit into modern eco-friendly packaging goals.
What Are Ad*Star Bags?
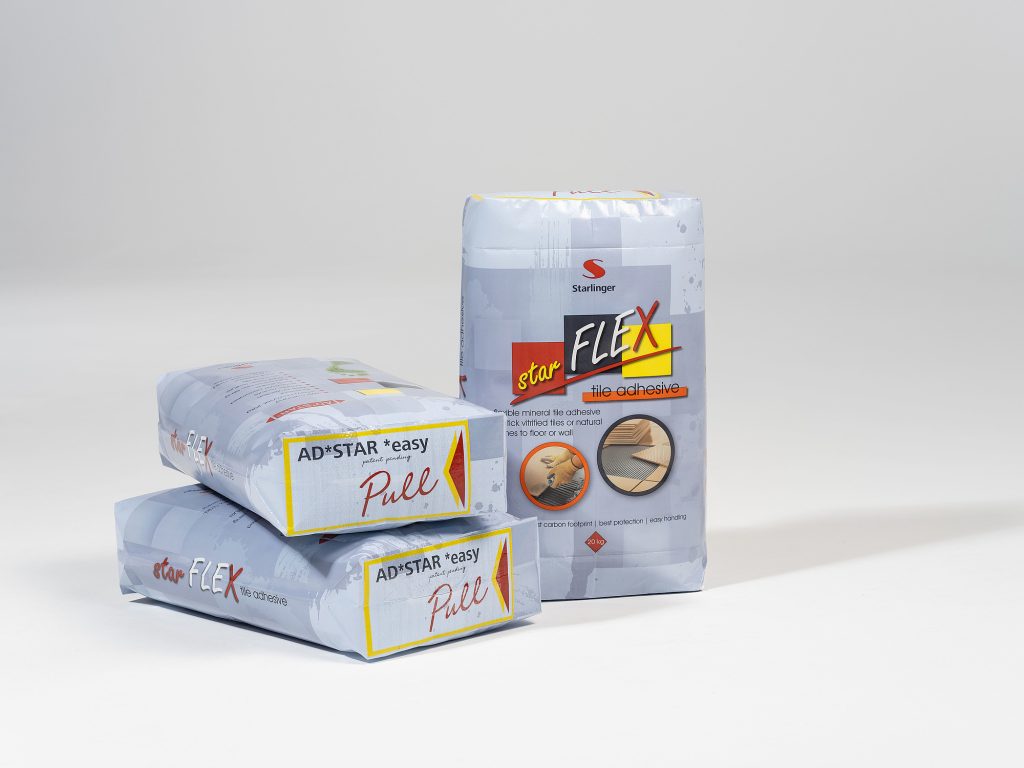
Ad*Star bags are patented block-bottom valve sacks made primarily from polypropylene (PP) fabric. They combine the durability of woven plastic with the printability and block-shape advantages often seen in paper bags. Developed for heavy-duty industrial packaging, they are known for being:
- 1. Tear-resistant
- 2. Moisture-proof
- 3. Stackable
- 4. Lightweight yet strong
Industries use them widely to package cement, fertilizers, pet food, chemicals, and even food grains.
Are Ad*Star Bags Recyclable?
Yes, Ad*Star Bags Are Recyclable—But There’s a Catch
Ad*Star bags are made from 100% polypropylene (PP), which is a thermoplastic polymer widely accepted in recycling streams. Because they are mono-material (made from a single plastic type), they are technically recyclable.
However, the recyclability of Ad*Star bags depends on several factors:
- 1. Cleanliness: Bags must be free of residue (cement, chemicals, or grains) to be accepted by most recyclers.
- 2. Recycling infrastructure: Facilities must be equipped to handle woven PP materials, which may differ from typical plastic containers or films.
- 3. Sorting: The bags must be sorted properly by polymer type to avoid contamination in recycling batches.
So while the material is recyclable, actual recycling rates vary based on local facilities and practices.
How Ad*Star Bags Support Eco-Friendly Packaging Goals
Despite the challenges, Ad*Star bags offer several environmental advantages:
1. Reduced Material Usage
Ad*Star bags are lightweight yet strong, meaning less plastic is needed to achieve the same level of protection compared to traditional multi-layer packaging.
2. Reusable Before Disposal
Their strength and durability allow for multiple uses before they are finally discarded. Some industries repurpose them for storage or transport.
3. Better Stackability = Lower Transport Emissions
The block-bottom design improves stacking efficiency, which reduces space during transportation and helps lower carbon emissions.
4. Lower Breakage Rates
Fewer torn or damaged bags mean less product waste—especially important for packaging cement, fertilizers, or food items.
Challenges to Recycling Ad*Star Bags
While Ad*Star bags are made from polypropylene (PP)—a material that is technically recyclable—they face several real-world challenges that hinder their recycling at scale. These challenges are not due to the material itself, but rather to systemic and practical issues in the waste management and recycling ecosystem.
1. Lack of Awareness Among End-Users
One of the most significant barriers to recycling Ad*Star bags is the lack of awareness among those who use them. These bags are commonly employed in sectors such as construction, agriculture, chemicals, and food packaging—industries that often operate in rural or industrial areas. In such settings, environmental awareness and waste segregation practices are typically low.
As a result, many users simply discard used Ad*Star bags as general waste, often sending them to landfills or leaving them exposed in the environment. The fact that these bags are reusable and recyclable is often not communicated clearly, especially to laborers or small-scale distributors who handle them daily. This lack of education about proper disposal means a significant portion of potentially recyclable material is lost.
2. Residue Contamination
Even when users intend to recycle, residue contamination presents a major obstacle. Ad*Star bags are frequently used to store or transport cement, fertilizers, chemicals, or food grains—all of which can leave stubborn residues behind. Recyclers require relatively clean plastic material for processing, and dirty or contaminated bags are often rejected outright.
Cleaning these bags before recycling can be time-consuming and resource-intensive, which discourages both individual users and recycling facilities from taking the extra effort. The leftover cement dust, chemical traces, or organic residue not only degrade the quality of the recycled plastic but can also pose health risks to recycling workers. This is why many recyclers either refuse to accept these bags or charge extra fees to process them.
3. Limited Collection and Processing Infrastructure
Another core issue is the limited availability of collection and recycling infrastructure capable of handling woven polypropylene materials. Most recycling facilities are set up to process more common household plastics like PET bottles or HDPE containers. Woven PP bags, especially when used in industrial applications, require specialized sorting, shredding, and extrusion machinery that is not widely available across all regions.
In many countries, especially in rural India or developing areas, municipal waste systems do not include PP woven bags in their recycling streams. Without accessible collection points or partnerships between private recyclers and local governments, even well-intentioned users may have no choice but to dispose of the bags improperly.
Alternatives and Innovations
In response to the growing demand for sustainable packaging, some forward-thinking manufacturers are actively innovating to make Ad*Star bags more environmentally friendly. One promising development is the use of biodegradable coatings that can break down more easily in the environment, reducing long-term plastic pollution. While polypropylene (PP) itself is not biodegradable, these coatings aim to mitigate the environmental footprint of the outer layers, especially when the bags end up in landfills or natural ecosystems.
Another important advancement is the incorporation of recycled polypropylene fibers into the production of new Ad*Star bags. By using post-consumer or post-industrial recycled plastic, companies can significantly cut down on virgin plastic consumption, conserve natural resources, and reduce the overall carbon footprint of manufacturing. This also supports a more circular economy model, where materials are reused rather than discarded after a single use.
In addition, the concept of “design for recycling” is gaining momentum. This involves rethinking every stage of the bag’s design—from structure and materials to labeling and adhesives—to ensure that the final product can be easily and efficiently recycled. For instance, avoiding mixed materials, inks, or laminates that complicate the recycling process can make a big difference in end-of-life outcomes.
Beyond materials, companies are also piloting buy-back and bag return programs to help recover used Ad*Star bags directly from consumers and businesses. These initiatives encourage users to return bags to designated collection points instead of discarding them, allowing manufacturers or recyclers to handle proper cleaning and recycling. When scaled effectively, such programs can close the loop, reduce environmental impact, and promote a culture of responsibility in industrial packaging.
Together, these innovations represent a meaningful step toward making Ad*Star bags not just durable and functional, but also truly sustainable in the long run.
Also Read: From Factory to Landfill: The Full Life Cycle Analysis of an Ad*Star Bag
Conclusion
So, are Ad*Star bags recyclable? Yes—but with conditions. Made from recyclable polypropylene, they offer a more eco-conscious option than multi-layer or mixed-material industrial sacks. However, for them to fulfill their sustainable promise, proper handling, cleaning, and recycling infrastructure are essential.
With growing global focus on sustainability, Ad*Star bags are poised to play a significant role in eco-friendly packaging solutions—especially when combined with recycling initiatives and responsible consumer practices.