Ad Star bags have gained significant popularity in the world of industrial packaging. Known for their durability, strength, and versatility, they are widely used across various industries such as agriculture, construction, and chemicals. But what makes these bags stand out? A large part of their effectiveness lies in the precise and intricate manufacturing process that ensures their superior quality. This blog post delves into the step-by-step process of how Ad Star bags are made, providing a comprehensive understanding of their creation.
What Are Ad Star Bags?
Before exploring the manufacturing process, it’s important to understand what Ad Star bags are. Ad Star bags are woven polypropylene bags designed using advanced technology, providing a robust, lightweight, and durable packaging solution. They are especially known for their block-bottom design, which allows for efficient stacking and transportation. These bags are commonly used to package materials such as cement, fertilizer, animal feed, and other granular products.
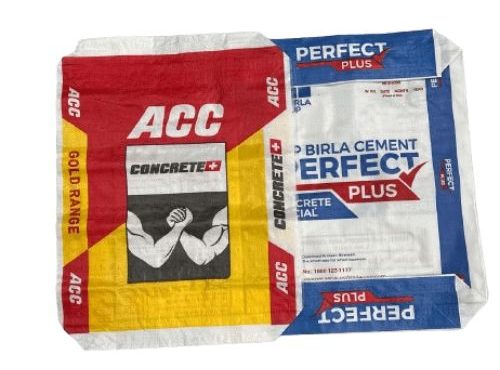
The Importance of Manufacturing Quality
The strength and durability of Ad Star bags are a direct result of their meticulous manufacturing process. Quality control during production is essential to ensure that each bag can withstand the rigors of transportation and storage. This attention to detail not only extends the lifespan of the bags but also ensures that the products inside remain protected. Understanding the production stages helps to appreciate the technical advancements and quality measures that go into each Ad Star bag.
Step-by-Step Manufacturing Process of Ad Star Bags
The creation of Ad Star bags involves several key stages, from the initial weaving of polypropylene tapes to the final quality control checks. Each stage contributes to the durability and functionality of the bags. Let’s break down this process:
1. Polypropylene Extrusion and Tape Production
The manufacturing process begins with polypropylene extrusion. Polypropylene, a type of plastic polymer, is melted and extruded into thin, flat tapes. These tapes serve as the foundation of the woven fabric used in Ad Star bags.
- Polymer Melting: The polypropylene granules are heated until they reach a molten state.
- Extrusion: The molten polypropylene is then extruded through a narrow die, creating long, thin tapes.
- Stretching: These tapes are stretched to align the molecular structure, which enhances their tensile strength. This stretching process is crucial for the durability of the woven fabric.
- Cooling and Winding: After stretching, the tapes are cooled and wound onto bobbins, ready for the next stage of weaving.
2. Weaving the Fabric
The woven fabric gives Ad Star bags their characteristic strength and flexibility. The process involves weaving the polypropylene tapes into a durable, breathable fabric.
- Circular Weaving Machines: The woven tapes are fed into circular weaving machines to create seamless, cylindrical fabric. This fabric forms the base of the Ad Star bag, offering high strength while remaining lightweight.
- Fabric Density: The density of the weave is carefully controlled to ensure optimal strength. A denser weave provides a stronger bag but may reduce breathability, making it essential to balance these factors depending on the intended use of the bag.
3. Lamination for Added Protection
After weaving, the fabric undergoes lamination. This step involves applying a thin layer of polypropylene or polyethylene film to the woven fabric, enhancing the bag’s resistance to moisture and external contaminants.
- Extrusion Coating: The film is applied using an extrusion coating technique, which ensures a uniform and strong bond with the woven fabric.
- Moisture Resistance: The lamination process makes the bags suitable for packaging moisture-sensitive products, such as cement and fertilizers, by preventing moisture ingress.
4. Cutting and Printing
Once the laminated woven fabric is prepared, it is cut into the desired sizes based on the dimensions of the Ad Star bags.
- Precision Cutting: Automated cutting machines ensure precise cuts, which are crucial for maintaining the uniformity and integrity of the bags.
- Printing: Custom printing is often added to the bags at this stage, allowing manufacturers to include logos, branding, or product information. This step is important for marketing and identification during transportation.
5. Block-Bottom Formation
One of the defining features of Ad Star bags is their block-bottom design, which allows the bags to stand upright and provides better stability.
- Bottom Folding: The cut pieces of fabric are folded and sealed to create a sturdy block bottom. This design ensures that the bags can hold their shape when filled, making them ideal for stacking and palletization.
- Hot Air Welding: The bottom is sealed using hot air welding, which creates a strong bond without the need for stitching. This technique not only increases the strength of the bags but also prevents any leakage of the packaged material.
6. Bag Conversion and Sewing
The cut and folded pieces are then converted into finished bags through a process called conversion. This stage involves forming the bag’s body and ensuring that it is securely joined.
- Tube Conversion: The fabric is converted into a tubular shape, with one end left open for filling.
- Sewing (if required): In some cases, the top of the bag may be sewn for additional reinforcement, especially for bags intended to carry heavy materials.
Quality Control and Testing
The final stage of the manufacturing process is quality control. Given the critical role of Ad Star bags in protecting and transporting products, manufacturers conduct thorough testing to ensure that the bags meet required standards.
1. Strength and Tear Testing
Quality control involves testing the tensile strength and tear resistance of the bags. This ensures that the bags can withstand rough handling and the weight of the materials they carry without breaking.
2. Drop and Compression Tests
Ad Star bags undergo drop tests and compression tests to simulate the conditions they might face during transportation. This ensures that the bags can maintain their integrity even when stacked in warehouses or dropped during handling.
3. UV Stability Testing
For bags that will be stored outdoors, UV stability testing is crucial. This test ensures that the bags do not degrade quickly when exposed to sunlight, maintaining their strength and durability over time.
Environmental Considerations in Manufacturing
As industries move toward more sustainable practices, the manufacturing process of Ad Star bags has also evolved to become more eco-friendly. Polypropylene is a recyclable material, and many manufacturers now implement practices to reduce waste during production.
- Recycling Scrap Material: Any leftover material or defective bags are often recycled back into the production process, reducing waste.
- Energy-Efficient Production: Advances in machinery have made the production process more energy-efficient, reducing the environmental footprint of Ad Star bag manufacturing.
Conclusion
The manufacturing process of Ad Star bags is a blend of precision engineering and advanced technology, resulting in a packaging solution that is both strong and versatile. From the extrusion of polypropylene tapes to the formation of the signature block-bottom design, each step ensures that these bags meet the highest standards of quality and performance. Understanding this process allows businesses to make informed decisions when choosing the right packaging solution for their needs, appreciating the craftsmanship that goes into each Ad Star bag.
Whether you are in the agriculture sector looking for a reliable storage solution or in the construction industry needing durable packaging, Ad Star bags offer a proven option. Their manufacturing process is a testament to the innovation and expertise that goes into creating a product that truly stands the test of time.